The global IoT in manufacturing market is rapidly growing, with its size expected to increase from USD 65.81 billion in 2024 to USD 181.86 billion by 2034, at a CAGR of 10.7%, according to Presedence Research.
IoT in manufacturing connects machines, devices, and systems to provide real-time data for better decision-making. Predictive maintenance and quality control are two key areas where IoT is having a profound impact.
Predictive maintenance helps identify equipment issues before they occur, reducing downtime and maintenance costs. IoT services in quality control ensures consistent product quality by monitoring production processes in real-time, catching defects early.
The long-term impact of IoT in manufacturing goes beyond efficiency. It enables manufacturers to boost productivity, reduce waste, and maintain high-quality standards, providing them with a significant competitive advantage in the industry.
Next, we’ll explore how IoT is transforming predictive maintenance and quality control in detail.
Role of IoT in transforming manufacturing
Manufacturers can collect and analyze data in real time, providing deeper visibility into operations by embedding sensors and smart devices into machines and production lines.
This shift is more than just automation—it's a complete transformation in how factories operate, making them smarter, more efficient, and cost-effective.
Connecting machines, processes, and people for better outcomes
One of the key benefits of IoT is its ability to connect machines, processes, and people in a unified system. Machines equipped with IoT sensors communicate data back to centralized platforms, providing updates on performance and potential failures.
This connection extends to workers as well, who can access real-time information to make quicker, informed decisions. The result is smoother workflows, fewer disruptions, and a more responsive strategy to addressing challenges.
Real-time data and actionable insights drives decision-making
At the heart of IoT’s impact is real-time data. IoT devices constantly monitor everything from machine health to production quality, feeding this data into systems that generate actionable insights.
These insights let manufacturers optimize processes, predict potential failures through IoT predictive maintenance, and ensure products meet required standards through IoT in quality control.
Key components of IoT in manufacturing
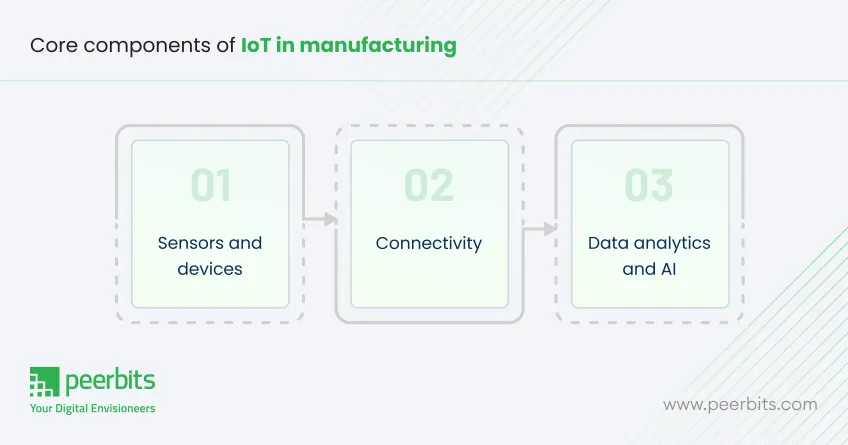
The effective implementation of IoT in manufacturing depends on a few key components that work together to optimize operations, improve efficiency, and reduce costs.
These elements helps with real-time monitoring, actionable insights, and smooth communication across the entire manufacturing process.
1. Sensors and devices
Sensors and IoT devices play an important role in monitoring machines and equipment in real-time. These devices collect data on parameters such as temperature, vibration, and pressure, providing insights into machine health and operational performance.
This constant flow of data lets manufacturers to implement IoT-based predictive maintenance, detecting issues before they lead to equipment failure. Manufacturers can minimize downtime and reduce maintenance costs by tracking the performance of machinery continuously.
2. Connectivity
Connectivity is the backbone of IoT that helps with smooth communication between devices, machines, and systems. Wireless networks such as 5G and Low Power Wide Area Networks (LPWAN) are essential for transmitting the large volumes of data generated by IoT sensors.
Reliable and fast connectivity ensures that real-time data can be accessed and acted upon without delays. This constant flow of information is essential for implementing IoT in quality control and maintaining efficiency across production lines.
3. Data analytics and AI
Once the data is gathered, advanced data analytics and artificial intelligence (AI) tools process and analyze it to provide meaningful insights. These insights help manufacturers make smarter decisions by identifying patterns, predicting equipment failures, and optimizing production workflows.
With IoT predictive maintenance, AI models can predict when machines are likely to fail, authorizing for timely maintenance scheduling. This reduces downtime, cuts operational costs, and boosts productivity.
In the next section, we will examine how IoT is applied to predictive maintenance and quality control in the manufacturing industry.
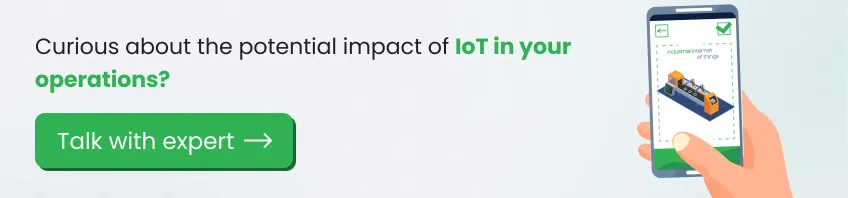
IoT in predictive maintenance: Managing equipment efficiently
Predictive maintenance has become a game changer in modern manufacturing. It lets manufacturers predict potential equipment failures before they happen, ensuring that machinery operates at its peak performance for longer periods.
Manufacturers can avoid unexpected downtime, reduce repair costs, and extend the lifespan of their equipment by identifying and addressing issues early.
Benefits of predictive maintenance
The most significant benefits of IoT-based predictive maintenance are reducing downtime and saving costs. With real-time monitoring, manufacturers can avoid unplanned shutdowns, which can disrupt production and result in costly repairs.
They also extend the lifespan of their equipment by predicting and addressing issues early. Predictive maintenance helps improve operational efficiency, reduce maintenance expenses, and ensure smoother manufacturing operations.
How predictive maintenance works using IoT?
Predictive maintenance using IoT involves real-time monitoring of equipment through sensors. This data helps predict potential failures, letting timely maintenance and reducing downtime.
1. Real-time monitoring and data collection
Real-time monitoring is the foundation of IoT-based predictive maintenance. Sensors embedded in machinery continuously collect data on performance metrics, such as vibrations, temperature, and power consumption.
This data is sent to centralized systems for analysis, where any deviations from normal operation are flagged for further investigation.
2. Data analytics and machine learning
Once the data is collected, it is analyzed using advanced data analytics and machine learning algorithms. These tools can detect patterns in the data, identify potential failures, and predict when maintenance should be scheduled.
Through continuous learning, these models become more accurate over time, helping manufacturers predict failures with greater precision.
3. Decision-making
With actionable insights from the data, manufacturers can make informed decisions about when to perform maintenance. Predictive maintenance lets them schedule maintenance during planned downtime, preventing unscheduled disruptions.
This strategy helps optimize maintenance resources, ensures minimal production downtime, and improves equipment reliability.
In the next section, we will discuss how IoT plays a key role in quality control in manufacturing.
Quality control in manufacturing: Maintaining consistency & precision
Maintaining high-quality standards is essential for the success of any manufacturing operation. Consistent product quality builds customer trust, reduces waste, and improves operational efficiency. Implementing IoT in quality management provides manufacturers with tools to achieve these goals effectively.
How IoT improves product quality by monitoring consistency
IoT in quality control improves precision by monitoring every stage of production. Sensors track key metrics such as temperature, pressure, and humidity in real time, ensuring that manufacturing conditions remain within acceptable limits.
This strategy minimizes deviations that could compromise product quality.
Real-time quality monitoring with IoT sensors
IoT sensors help with real-time quality control by identifying defects as they occur. For instance, sensors can detect anomalies in product dimensions, surface quality, or material composition.
This immediate feedback lets manufacturers correct issues before they impact an entire production batch, significantly reducing waste and maintaining consistent standards.
In the next section, we’ll explore the challenges manufacturers face when implementing IoT-based quality management systems.
How IoT predictive maintenance supports quality control in manufacturing
Combining predictive maintenance and quality control in manufacturing enhances efficiency and consistency. This integration helps manufacturers maintain equipment reliability while ensuring products meet quality standards.
The table below illustrates how these two aspects complement each other.
Aspect | Predictive maintenance | Quality control | Combined benefits |
---|---|---|---|
Primary goal | Identifying equipment issues before they cause breakdowns | Maintaining consistent product quality by detecting defects | Reduces downtime and ensures consistent output |
IoT role | Sensors collect data on machine performance to predict failures | Sensors monitor production processes to maintain quality standards | Unified tracking of equipment performance and product quality |
Predictive analytics impact | Schedules maintenance tasks based on data to avoid disruptions | Identifies potential production issues early to maintain quality | Synchronizes equipment maintenance with quality assurance for smoother operations |
Application of IoT for maintenance and quality control
A manufacturing line could use IoT sensors to monitor both machinery and production quality. For instance, temperature sensors might detect overheating in a molding machine while other sensors verify the dimensions of the molded product.
This combined monitoring ensures machines operate efficiently and products meet standards.
Data-driven future of manufacturing
IoT is making a future where manufacturing heavily depends on data for improved efficiency. Technologies like big data, edge computing, along with AI development services are redefining operations and productivity.
Big data and IoT
- Big data analytics is becoming essential for modern manufacturing processes.
- Information from IoT devices is analyzed to predict failures and refine workflows.
Edge computing
- Edge computing processes information closer to its source, minimizing delays.
- This helps with faster decisions in critical manufacturing activities.
AI and machine learning
- Combining AI with IoT helps refine predictions and monitor quality with precision.
- Machine learning evaluates IoT data to deliver insights that support efficient production and maintenance.
These advancements are turning manufacturing into a more efficient and precise industry.
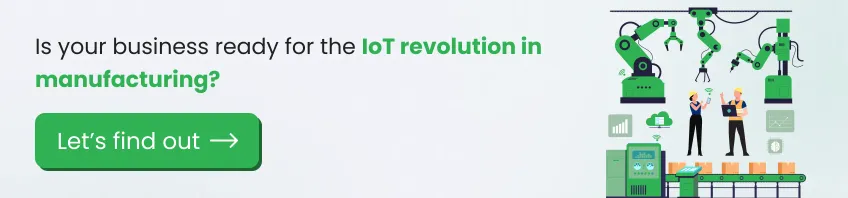
Challenges of implementing IoT in maintenance and quality control
While IoT offers significant benefits, its implementation in predictive maintenance and quality control comes with certain challenges that manufacturers must address.
1. High initial costs
- Setting up IoT systems involves investing in devices, sensors, and network infrastructure.
- Small to medium-sized manufacturers may face budget constraints during the initial stages.
2. Data management and analysis
- IoT systems generate massive amounts of data that need proper organization and interpretation.
- Extracting actionable insights requires advanced tools and efficient processing systems.
3. Skilled workforce
- Employees need to be trained to operate IoT systems and analyze the resulting data.
- This requires time and resources, which can be challenging for some organizations.
4. Integration with legacy systems
- Many manufacturers rely on older equipment that lacks smart capabilities.
- Incorporating IoT solutions with these systems often requires additional customization and resources.
5. Cybersecurity risks
- IoT systems are vulnerable to potential cyberattacks that can compromise sensitive operational data.
- Securing IoT networks is essential to protect the integrity of manufacturing processes.
Addressing these challenges is important to fully utilize the potential of IoT in manufacturing.
Sustainability in IoT manufacturing
IoT contributes to making manufacturing processes more environmentally friendly and resource-efficient. It supports businesses in achieving productivity while reducing their ecological impact.
1. How IoT supports sustainable manufacturing
- IoT systems monitor operations in real-time, helping reduce resource waste.
- Energy consumption is adjusted based on usage patterns, improving efficiency.
- Environmental impact is minimized by identifying areas for improvement in production workflows.
2. Real-time monitoring for sustainability
- Sensors track energy usage, highlighting opportunities for conservation.
- Waste is reduced by monitoring raw material utilization and addressing inefficiencies.
- IoT systems track emissions, enabling manufacturers to meet regulatory standards.
3. IoT in waste and energy management
According to ScienceDirect, IoT technologies such as LPWAN, LoRaWAN, and real-time cloud platforms are transforming waste and energy management in manufacturing. These advancements facilitate monitoring resource consumption, optimizing disposal schedules, and minimizing energy usage.
Inspired by smart city systems, these technologies align production processes with sustainability goals, reducing both environmental impact and operational inefficiencies.
Guide to implement IoT manufacturing in your business
Laying the foundation for IoT adoption requires careful planning and strategic execution. Here’s a step-by-step guide:
Step 1: Define objectives
Identify the challenges you want to tackle, such as equipment maintenance, quality assurance, or energy optimization. Clear goals guide technology selection and implementation.
Step 2: Assess current infrastructure
Evaluate your existing machinery, network systems, and data collection capabilities. This ensures the compatibility of IoT solutions with your operations.
Step 3: Select suitable technologies
Choose IoT sensors, analytics tools, and connectivity options like LPWAN or 5G. Ensure the technology is scalable for future growth and evolving demands.
Step 4: Allocate a budget
Plan for initial investment, recurring costs for maintenance, and potential upgrades. Having a well-defined budget helps in balancing innovation with cost-effectiveness.
Step 5: Develop a phased implementation plan
Begin with a small-scale project targeting a single operation, such as predictive maintenance. Test the results, gather insights, and expand gradually.
Step 6: Train your workforce
Provide training for employees to manage IoT systems and interpret data effectively. A well-trained workforce ensures successful adoption and usage.
Step 7: Monitor and optimize
Regularly analyze data generated by IoT systems. Use insights to make data-driven decisions and refine your processes for maximum efficiency.
Key considerations for successful IoT implementation
When adopting IoT, keep these factors in mind to ensure a smooth transition:
- Budget: Determine a realistic budget that covers implementation, training, and ongoing support.
- Technology selection: Opt for solutions that stick with your business goals and offer scalability for future growth.
- Scalability: Choose systems that can adapt to increasing demands without services.
Manufacturers can smoothly integrate IoT into their operations, boosting efficiency and long-term success by addressing these considerations alongside the step-by-step guide.
Cost considerations: Understanding the ROI of IoT
Implementing IoT in manufacturing requires understanding both initial costs and ongoing investments. Let’s break down the key components and how to assess ROI effectively.
Initial investment and ongoing costs
Implementing IoT in manufacturing involves upfront expenses like sensors, connectivity, and software, along with recurring costs for maintenance, data management, and energy usage.
Initial setup costs:
- IoT sensors and devices: These are crucial for monitoring equipment, detecting defects, and gathering data in real-time. The price varies depending on the complexity and scale of your operations.
- Connectivity infrastructure: Investments in reliable communication networks (e.g., 5G, LPWAN) are essential for seamless IoT integration. Software and data analytics: Platforms for analyzing IoT data and predictive maintenance solutions often require a one-time setup fee or licensing cost.
- Training and personnel: Skilled staff is essential for handling the technology. The training and hiring process can add to initial costs.
Ongoing maintenance and operational costs:
- System maintenance: IoT systems require regular updates, patching, and monitoring to ensure reliability and security.
- Data storage and processing: As IoT generates large volumes of data, cloud services or on-premise data storage solutions incur recurring costs.
- Energy costs: Some IoT devices may consume power, depending on their functionality and frequency of data transmission.
Calculating ROI for IoT solutions in predictive maintenance and quality control
1. Reduced downtime: Predictive maintenance minimizes unexpected breakdowns. By forecasting equipment failures, IoT helps schedule maintenance only when necessary, saving on unplanned downtime costs.
2. Extended equipment life: IoT can ensure timely repairs and optimize equipment lifespan, delaying costly replacements by continuously monitoring the health oof machinery.
3. Improved quality control: IoT sensors help in detecting defects early, reducing scrap rates and ensuring products meet quality standards. This leads to fewer returns and higher customer satisfaction.
4. Operational efficiency: Real-time data from IoT devices helps streamline operations, reducing waste and improving energy efficiency.
Future of IoT in manufacturing
The manufacturing industry is undergoing significant change as IoT technologies continue to develop. From integrating AI and 5G to creating fully automated smart factories, these advancements has the potential to change the way how businesses operate.
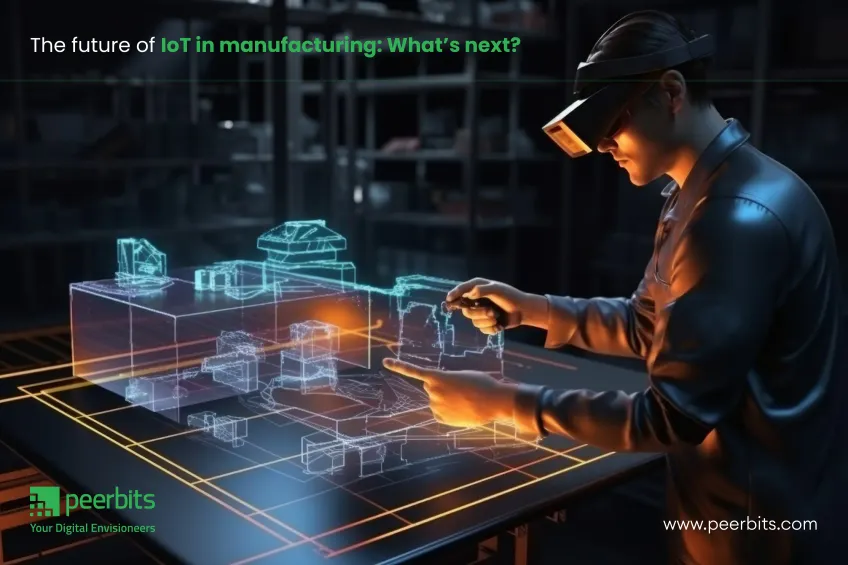
Advanced technologies redefining IoT in manufacturing
AI, blockchain, and 5G are becoming integral to the future of IoT in manufacturing. AI improves analytics by predicting equipment failures and streamlining operations with greater precision.
Blockchain ensures secure and transparent data exchange across supply chains. 5G technology facilitates faster, low-latency communication, which supports real-time decision-making and system integration.
Rise of fully automated smart factories
Smart factories, powered by interconnected IoT devices, are changing traditional manufacturing models. These factories use digital twins, collaborative robots (cobots), and automated systems to manage production with minimal human intervention.
Real-time data monitoring improves operational accuracy, while digital twins let businesses simulate and optimize production workflows. This level of automation improves efficiency and adaptability to market changes.
IoT as a competitive advantage
Incorporating latest IoT technologies can help manufacturers with maintaining. Predictive supply chain systems, powered by IoT, can improve operational efficiency, while technology-based eco-friendly practices stick with sustainability goals.
Manufacturers who integrate IoT into their operations will gain a stronger position to deliver high-quality products while reducing costs and addressing environmental concerns.
Conclusion
IoT has changed the way how manufacturers manage predictive maintenance and quality control. Businesses can anticipate equipment failures, addressing quality issues, and significantly reduce operational costs by connecting devices and gathering real-time data.
This data-based strategy provides manufacturers with a competitive advantage. Improved maintenance strategies and improved product quality result in increased efficiency, longer equipment lifespans, and superior output.
As AI, machine learning, and 5G advance, IoT will continue to develop, leading to even more efficient and reliable operations. For businesses seeking long-term success, adopting IoT is crucial.
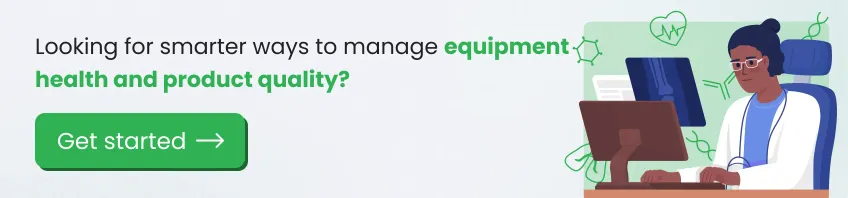
FAQ's
A digital twin is a virtual representation of a physical object or system. Using IoT sensors, it collects real-time data to simulate and optimize processes without interfering with production lines, making manufacturing more agile.
IoT devices, such as wearable sensors and smart monitoring systems, enhance safety by detecting harmful conditions like excessive heat, gas leaks, or unsafe practices. These insights allow manufacturers to create safer working environments.
Yes, IoT solutions are scalable and cost-effective for SMEs. Cloud-based IoT platforms and modular systems allow SMEs to adopt these technologies incrementally, aligning with their budgets and operational needs.
IoT ensures accurate product traceability by integrating RFID tags and sensors throughout the supply chain. This enables manufacturers to identify bottlenecks, reduce waste, and maintain quality standards seamlessly.
IoT-enabled energy management systems monitor consumption patterns and optimize machine usage. This reduces energy waste and lowers operational costs, promoting sustainability in manufacturing practices.
Yes, IoT systems can be vulnerable to cyber threats. Manufacturers should prioritize cybersecurity measures such as encrypted communication, regular updates, and access controls to safeguard their operations.